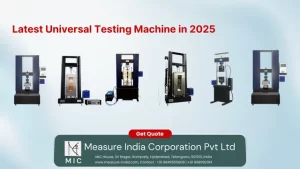
Working Principle of a Universal Testing Machine
A Universal Testing Machine (UTM) operates on a simple but powerful mechanical principle: it applies a controlled load or displacement to a test specimen and measures the resulting deformation or reaction force. This helps in analyzing the mechanical behavior of materials under various conditions like tension, compression, bending, or shear.
The working principle of a Universal Testing Machine (UTM) is centered around evaluating how materials respond under various types of load, such as tension and compression. The process begins with test specimen placement, where the material sample is clamped securely between two fixtures—grips for tensile tests and platens for compression tests. In a tensile test, the grips pull the specimen apart, while in a compression test, the platens apply force to squeeze the sample from both ends. After the specimen is fixed, the application of load takes place. This is achieved either through a motor-driven screw mechanism in electromechanical UTMs or a hydraulic actuator in hydraulic UTMs. The crosshead, which moves vertically, applies force depending on the test type, and a load cell precisely measures the force being exerted.
As the load is applied, the material begins to deform, which leads to the measurement of deformation. Instruments like extensometers or strain gauges are used to record how much the material stretches during tensile testing or compresses during compression testing. These instruments provide data on strain, while the applied force is recorded as stress. The UTM’s software then generates a real-time stress-strain curve, a graphical representation that highlights the material’s key mechanical properties. This includes the elastic limit, yield strength, ultimate tensile strength (UTS), Young’s modulus, and the fracture point. Finally, the test termination and result analysis step occurs automatically when the material either breaks or reaches a predefined load limit. The software compiles all test data for detailed review, offering engineers precise insights into the material’s performance characteristics. This makes Universal Testing essential in quality control, research, and material certification processes across industries.
The working of a Universal Testing Machine is based on well-established mechanical principles. First, it follows Newton’s Second Law of Motion (F = ma), which states that the force applied to a material results in acceleration or deformation. This principle allows the UTM to apply a measurable and controlled force on the test specimen. Secondly, the machine operates according to Hooke’s Law (σ = E·ε), which is valid within the material’s elastic limit. This law explains the linear relationship between stress (σ) and strain (ε), where E is the modulus of elasticity. It helps in understanding how materials return to their original shape after a small amount of deformation. Lastly, the UTM is guided by the Stress-Strain Theory, where the relationship between applied stress and the resulting strain is used to evaluate material behavior. This includes identifying key mechanical properties like yield strength, tensile strength, and fracture point. Together, these principles form the foundation of accurate and reliable material testing in both research and industrial applications.
Modern Universal Testing Machines (UTMs) utilize a closed-loop control system to ensure highly accurate and consistent loading during testing. This system continuously monitors and adjusts the applied force or displacement in real-time, allowing precise control over test conditions. Key components that make this possible include servo motors, which provide smooth and controlled motion of the crosshead; digital controllers, which interpret commands and adjust system behavior accordingly; and high-speed data acquisition systems, which capture stress, strain, and deformation data at very fine intervals. This advanced setup ensures that even the smallest material changes are detected and recorded, making modern UTMs ideal for high-precision research and quality control applications.
Universal Testing Machines (UTMs) play a crucial role in engineering and material science by providing accurate data that aids in precise material selection for engineering design. By evaluating mechanical properties such as strength, elasticity, and ductility, engineers can choose the most suitable material for a specific application. UTMs also ensure that materials and components meet international standards like ASTM and ISO, which is vital for safety and regulatory compliance across industries. In high-stakes sectors such as aerospace and construction, UTMs support predictive failure analysis, helping to identify potential weak points before failure occurs. Additionally, they are indispensable tools in research and innovation, enabling scientists to develop and validate new materials with enhanced performance characteristics.
If you’re looking for the best Universal Testing Machine (UTM Machine) for your business, contact Measure India Corporation Pvt. Ltd. today for expert guidance and the best pricing options.
For more details, visit www.measure-india.com and explore our latest range of Universal Testing Machines!
Office Address : Universal Testing Machine Suppliers in India
MIC House, Sree Nagar, Rampally,
Hyderabad – 501301, Telangana, India
Website: www.measure-india.com
Phone: +91-9989921114
Email: info@measure-india.com