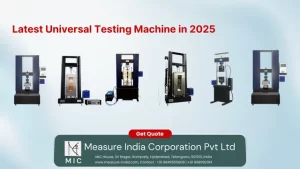
Fatigue Crack Growth: Understanding, Testing, and Industry Applications
Fatigue crack growth is a critical phenomenon in materials science and engineering. It refers to the slow progression of cracks in a material due to repeated stress cycles. This process is particularly significant in industries like aerospace, automotive, and construction, where material failure can have serious consequences. In this article, we will explore what fatigue crack growth is, the factors influencing it, testing methods, and its real-world applications.
What is Fatigue Crack Growth?
Fatigue crack growth occurs when a material is subjected to fluctuating stress over time, leading to microscopic cracks that gradually expand. If not controlled, these cracks can cause catastrophic failure. The study of fatigue crack growth helps engineers design more durable and reliable materials.
Factors Affecting Fatigue Crack Growth:
Stress Intensity – Higher stress accelerates crack propagation.
Material Properties – Different metals and composites have varying resistance to fatigue.
Environmental Conditions – Corrosion and temperature changes impact fatigue life.
Load Frequency – The rate of stress cycles affects crack growth speed.
Fatigue Crack Growth Rate & Paris’ Law
One of the most widely used formulas to predict fatigue crack growth is Paris’ Law, which expresses the crack growth rate as:
da/dN = Crack growth rate per cycle
C, m = Material-specific constants
ΔK = Stress intensity factor range
By analyzing this formula, engineers can estimate the remaining life of a component and determine necessary design modifications.
Several testing methods are used to evaluate fatigue crack growth in materials:
Universal Testing Machine (UTM) Fatigue Tests
Measures crack initiation and growth under cyclic loading.
Used for materials like steel, aluminum, and composites.
Learn more about Universal Testing Machines (UTMs).
Compact Tension (CT) Test
Standard method for measuring fatigue crack propagation.
Common in aerospace and automotive industries.
Fracture Mechanics Analysis
Uses Finite Element Analysis (FEA) to predict crack behavior.
Helps in failure prevention strategies.
Fatigue crack growth analysis is essential for ensuring the safety and durability of structures and components in various industries:
Aerospace: Prevents fatigue failure in aircraft wings and fuselage.
Automotive: Helps improve the durability of engine components and chassis.
Structural Engineering: Ensures bridges and buildings withstand long-term stress.
Manufacturing: Aids in material selection for high-performance applications.
Testing Laboratories: Uses UTM machines for fatigue and tensile testing.
Material Selection: Use alloys with high fatigue resistance.
Surface Treatments: Apply coatings to prevent crack initiation.
Optimized Design: Reduce stress concentration points in structures.
Regular Inspection: Use non-destructive testing (NDT) to detect early cracks.
Advanced Testing with Universal Testing Machines (UTMs): Helps evaluate material fatigue resistance and ensures safety.
Conclusion
Fatigue crack growth is a major concern in engineering, and understanding its behavior is crucial for preventing failures. With advanced testing techniques like UTM-based fatigue testing and fracture mechanics analysis, industries can enhance material durability and improve safety.
Want to learn more about fatigue testing solutions? Contact us today! 🚀
Office Address : Fatigue Testing Machine Supplier in India
MIC House, Sree Nagar, Ram pally,
Hyderabad – 501301, Telangana, India
Website: www.measure-india.com
Phone: +91-9989921114
Email: info@measure-india.com