Fatigue Testing
We have extensive experience across a wide range of industries
Fatigue Testing: Importance, Process & Applications
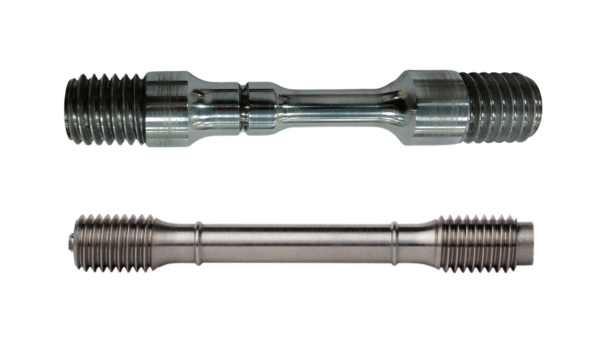
Fatigue testing is a crucial method used in engineering and material science to determine how a material behaves under repeated cyclic loading. This testing helps in predicting the lifespan of components used in industries like aerospace, automotive, and manufacturing, ensuring durability and safety.
What is Fatigue Testing?
Fatigue testing is a mechanical test conducted to evaluate how a material or component withstands repeated stress over time. This test simulates real-world conditions where materials experience fluctuating loads, helping engineers design reliable and durable products.
Why is Fatigue Testing Important?
Predicts Material Failure: Identifies weak points in materials before they fail.
Enhances Safety: Ensures components used in critical applications remain reliable.
Optimizes Design: Helps engineers improve product designs for better performance.
Reduces Maintenance Costs: Prevents unexpected failures, reducing repair and replacement costs.
Fatigue Testing Process
Specimen Preparation: A sample of the material is prepared according to testing standards.
Loading Application: The specimen undergoes cyclic loading with controlled force.
Stress Variations: Different stress levels are applied to determine endurance limits.
Crack Initiation & Propagation: The test identifies when and how cracks develop.
Failure Analysis: Data is collected to assess the material’s fatigue life.
Types of Fatigue Testing
High-Cycle Fatigue Testing: Conducted at low stress with a high number of cycles.
Low-Cycle Fatigue Testing: Performed under high stress with fewer cycles.
Thermal Fatigue Testing: Evaluates materials under varying temperature conditions.
Rotating Bending Fatigue Testing: Used for components like shafts and turbines.
Applications of Fatigue Testing
Aerospace Industry: Ensures aircraft components withstand repeated stress.
Automotive Industry: Tests durability of engine parts, suspension systems, and chassis.
Medical Devices: Evaluates the lifespan of implants and prosthetics.
Power Generation: Ensures reliability of turbine blades and generators.
Construction Materials: Tests steel, concrete, and other materials used in infrastructure.
Conclusion
Fatigue testing is essential for designing long-lasting and safe products across multiple industries. By understanding how materials behave under cyclic loading, engineers can prevent failures, improve designs, and enhance product reliability.
Fatigue Testing – FAQs
1. What are the different types of fatigue test specimens used in axial and bending fatigue testing?
Fatigue testing specimens are designed based on testing requirements and material properties. The most common types include:
Round Specimens – Used for axial fatigue and rotating bending fatigue tests.
Flat Specimens – Preferred for sheet metals and composite materials.
Notched Specimens – Used to study crack initiation and propagation in high-stress areas.
Wire & Fiber Specimens – Designed for fatigue testing of thin wires, ropes, and composite fibers.
Choosing the right specimen type ensures accurate fatigue life prediction and failure analysis.
2. Why is surface finish critical in fatigue testing sample preparation?
Surface finish plays a crucial role in fatigue testing as rough or uneven surfaces can introduce stress concentrations, leading to premature fatigue failure. Polished specimens help in:
Reducing micro-cracks that can affect fatigue life.
Ensuring uniform stress distribution during cyclic loading.
Complying with international fatigue testing standards like ASTM E466 and ISO 12106.
For accurate fatigue testing results, precision machining and proper surface preparation are essential.
3. How are fatigue test specimens prepared as per ASTM and ISO standards?
Fatigue testing specimens are machined with precision following industry standards such as:
ASTM E466 – Axial fatigue testing for metallic materials.
ASTM E606 – Low cycle fatigue (LCF) testing.
ISO 12106 – Fatigue testing of metallic materials under strain-controlled conditions.
Standardized preparation ensures repeatability, accurate fatigue life estimation, and compliance with global testing standards.
4. What factors influence fatigue specimen design and testing accuracy?
Several factors impact fatigue specimen performance and test accuracy, including:
Material Properties – Strength, ductility, and grain structure affect fatigue resistance.
Stress Concentration Points – Notched vs. unnotched designs influence crack initiation.
Loading Conditions – Axial, bending, or torsional fatigue tests determine specimen shape.
Machining Precision – Poor alignment or surface defects can lead to early failure.
Proper fatigue test specimen design helps in reliable fatigue failure analysis and component life prediction.
5. Can fatigue testing be performed on coated, heat-treated, or surface-treated materials?
Yes, fatigue testing is commonly conducted on coated, heat-treated, or surface-modified materials to evaluate their durability under cyclic loading. Key considerations include:
Coating Thickness – May impact fatigue life and crack propagation.
Heat Treatment Effects – Alters material hardness and fatigue strength.
Surface Treatments (Shot Peening, Nitriding, etc.) – Can enhance fatigue resistance.
Testing surface-treated materials helps industries improve product durability and fatigue performance in real-world applications.
Looking for fatigue testing services in India? Get accurate, NABL-certified material testing with advanced Universal Testing Machines (UTMs) today!
How Fatigue Testing Works – Process & Importance
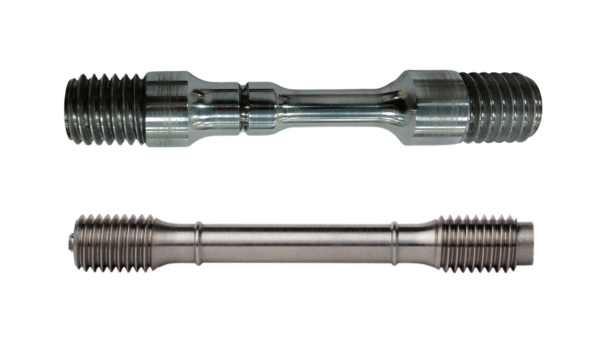
At MIC Labs, maintaining a well-structured Quality sample preparation plays a key role in generating accurate and repeatable test data. Keeping this in view, MIC Labs initiated the establishment of its own sample preparation workshop in 2023. Over time, we have developed a state-of-the-art machining center to extract, prepare, and polish test specimens according to various ASTM, ISO, and IS testing standards.
Our experienced machinists are highly skilled in preparing specimens with tight tolerances as required by the aerospace, defense, manufacturing industries, crucial research projects, and academic programs.
The in-house workshop has also enabled MIC Labs to undertake high-volume testing contracts while ensuring quality and timely deliverables.
Fatigue Testing Process
Sample Preparation
A standardized specimen is prepared based on global testing standards such as ASTM E466 (for axial fatigue testing), ASTM E606 (for low cycle fatigue), and ISO 12106 (for metallic materials). The specimen types depend on the material and testing method and can include:
Round Specimen – Used for axial and rotating bending fatigue tests.
Flat Specimen – Preferred for sheet materials and certain high-cycle fatigue applications.
Notched Specimen – Designed to study fatigue crack initiation and propagation.
Wire & Fiber Specimen – Used for fatigue testing of thin wires and composite fibers.
Proper machining, surface finish, and alignment are critical to obtaining accurate and repeatable fatigue test results while minimizing stress concentrations and premature failure
Fatigue Testing Sample Preparation – FAQs
1. What are the different types of fatigue test specimens used in axial and bending fatigue testing?
Fatigue testing specimens are designed based on testing requirements and material properties. The most common types include:
Round Specimens – Used for axial fatigue and rotating bending fatigue tests.
Flat Specimens – Preferred for sheet metals and composite materials.
Notched Specimens – Used to study crack initiation and propagation in high-stress areas.
Wire & Fiber Specimens – Designed for fatigue testing of thin wires, ropes, and composite fibers.
Choosing the right specimen type ensures accurate fatigue life prediction and failure analysis.
2. Why is surface finish critical in fatigue testing sample preparation?
Surface finish plays a crucial role in fatigue testing as rough or uneven surfaces can introduce stress concentrations, leading to premature fatigue failure. Polished specimens help in:
Reducing micro-cracks that can affect fatigue life.
Ensuring uniform stress distribution during cyclic loading.
Complying with international fatigue testing standards like ASTM E466 and ISO 12106.
For accurate fatigue testing results, precision machining and proper surface preparation are essential.
3. How are fatigue test specimens prepared as per ASTM and ISO standards?
Fatigue testing specimens are machined with precision following industry standards such as:
ASTM E466 – Axial fatigue testing for metallic materials.
ASTM E606 – Low cycle fatigue (LCF) testing.
ISO 12106 – Fatigue testing of metallic materials under strain-controlled conditions.
Standardized preparation ensures repeatability, accurate fatigue life estimation, and compliance with global testing standards.
4. What factors influence fatigue specimen design and testing accuracy?
Several factors impact fatigue specimen performance and test accuracy, including:
Material Properties – Strength, ductility, and grain structure affect fatigue resistance.
Stress Concentration Points – Notched vs. unnotched designs influence crack initiation.
Loading Conditions – Axial, bending, or torsional fatigue tests determine specimen shape.
Machining Precision – Poor alignment or surface defects can lead to early failure.
Proper fatigue test specimen design helps in reliable fatigue failure analysis and component life prediction.
5. Can fatigue testing be performed on coated, heat-treated, or surface-treated materials?
Yes, fatigue testing is commonly conducted on coated, heat-treated, or surface-modified materials to evaluate their durability under cyclic loading. Key considerations include:
Coating Thickness – May impact fatigue life and crack propagation.
Heat Treatment Effects – Alters material hardness and fatigue strength.
Surface Treatments (Shot Peening, Nitriding, etc.) – Can enhance fatigue resistance.
Testing surface-treated materials helps industries improve product durability and fatigue performance in real-world applications.
Looking for tensile testing services in India? Get accurate, NABL-certified material testing with advanced Universal Testing Machines (UTMs) today!
Fatigue Testing Gripping – Process & Importance
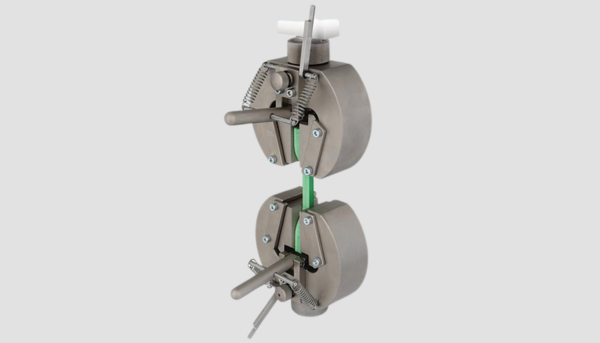
Testing materials according to various standards requires a wide range of grips and fixtures to securely hold specimens.
Keeping future requirements in mind, MIC Labs has been investing in developing a diverse range of grips and fixtures to accommodate all testing standards and material types.
MIC Labs’ inventory includes over 80 types of grips and fixtures designed for testing at low temperatures, room temperature, and high temperatures, covering a temperature range from -195°C to 1150°C.
Fatigue Testing Gripping Process
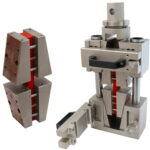
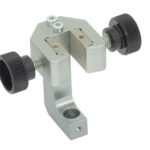
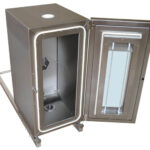
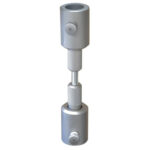
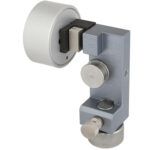
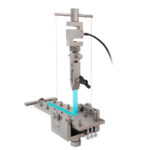
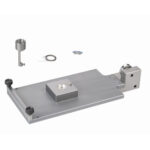
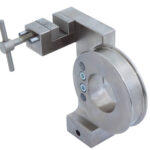
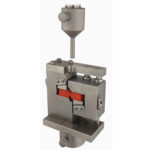

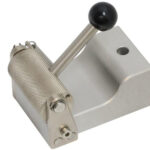

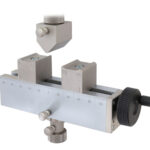
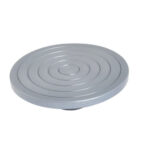
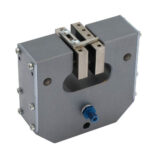
Specimen Alignment & Placement
The test specimen is positioned correctly to ensure axial loading and prevent bending stresses.
Alignment tools or guides may be used for precision placement.
Grip Selection Based on Material & Shape
Different types of grips are used depending on the material, thickness, and specimen shape:
- Wedge Grips – Self-tightening for metals and composites
- Hydraulic Grips – Uniform pressure distribution for high-strength materials
- Pneumatic Grips – Suitable for delicate materials like textiles and films
- Vice Grips – Basic mechanical clamping for simple applications
- Threaded/Pin Grips – Used for wires, rods, and rebar testing
Clamping the Specimen
- The grips are tightened to prevent movement without damaging the specimen.
- If required, serrated or textured grips enhance friction to prevent slippage.
Load Application & Monitoring
- The UTM applies a controlled increasing tensile force to the gripped specimen.
- Sensors monitor stress-strain behavior, ensuring precise measurements.
Fatigue Testing Gripping – FAQs
1. Why is proper gripping important in tensile testing?
Proper gripping ensures that the specimen remains securely held without slippage or premature failure at the grip points. This guarantees accurate stress-strain measurements during tensile testing.
2. What types of grips are used in a Universal Testing Machine (UTM)?
Common grip types include:
- Wedge Grips – Self-tightening, ideal for metals and composites
- Hydraulic Grips – Even pressure distribution for high-strength materials
- Pneumatic Grips – Used for thin or delicate materials like textiles and films
- Vice Grips – Simple and cost-effective for basic tensile tests
Threaded/Pin Grips – Designed for specific wire, rope, or rebar testing
3. How do you prevent specimen slippage during tensile testing?
To prevent slippage:
- Use textured or serrated grips for better friction
- Ensure proper grip pressure without damaging the sample
- Align the specimen correctly to avoid bending or off-axis loading
4. What is the role of self-aligning grips in tensile testing?
Self-aligning grips adjust to ensure that the load is applied uniformly along the specimen’s axis, preventing stress concentrations and inaccurate results.
5. How do hydraulic and pneumatic grips improve testing accuracy?
Hydraulic and pneumatic grips apply consistent and uniform clamping pressure, reducing manual errors and ensuring reliable tensile strength measurements, especially for high-strength or brittle materials.
Looking for Fatigue testing services in India? Get accurate, NABL-Certified material testing with advanced Universal Testing Machines (UTMs) today!
How Fatigue Testing Works – Process & Importance
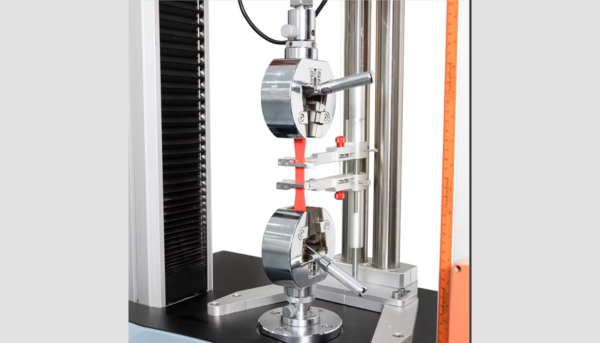
MIC Labs is equipped to test various materials under fatigue loading, ensuring compliance with the following standards:
ASTM E466 – Standard Practice for Conducting Force Controlled Constant Amplitude Axial Fatigue Tests of Metallic Materials
ASTM E606/E606M – Standard Test Method for Strain-Controlled Fatigue Testing
ISO 12106 – Metallic Materials – Fatigue Testing – Axial Strain-Controlled Method
ASTM D7791 – Standard Test Method for Uniaxial Fatigue Properties of Plastics
ISO 6721-4 – Plastics – Determination of Dynamic Mechanical Properties – Part 4: Tensile Fatigue
ASTM D3479 – Standard Test Method for Tension-Tension Fatigue of Polymer Matrix Composite Materials
These standards ensure that MIC Labs can accurately evaluate the fatigue life, durability, and performance of metallic, plastic, and composite materials under cyclic loading conditions.
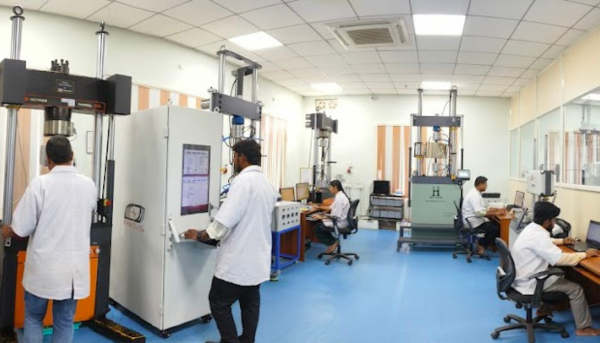
Fatigue Testing – FAQs
1. What is tensile testing, and why is it important?
Tensile testing is a material testing method that measures a material’s strength by applying a controlled tensile (pulling) force until it breaks. It helps determine ultimate tensile strength (UTS), yield strength, elongation, and ductility, making it essential for quality control and product development in industries like aerospace, automotive, and construction.
2. What materials can be tested in a tensile test?
Tensile testing is performed on various materials, including:
Metals & Alloys (Steel, Aluminum, Titanium – ASTM E8, ISO 6892)
Plastics & Polymers (ASTM D638, ISO 527)
Composites & Fibers (ASTM D3039, ISO 14125)
Rubber & Elastomers (ASTM D412, ISO 37)
Textiles & Films (ASTM D882, ISO 527-3)
3. What are the key parameters measured in tensile testing?
Tensile testing provides critical data, including:
Ultimate Tensile Strength (UTS): Maximum stress before fracture
Yield Strength: Stress at which permanent deformation starts
Elongation (%): Material stretchability before breaking
Young’s Modulus: Stiffness or elasticity of the material
Break Point: Load at which the material completely fractures
4. What standards are followed for tensile testing?
Tensile tests follow international standards to ensure consistency and accuracy:
ASTM E8 / ISO 6892 – Metals & Alloys
ASTM D638 / ISO 527 – Plastics & Polymers
ASTM D3039 – Composites
ASTM D882 – Thin Films & Textiles
5. How do Universal Testing Machines (UTMs) perform tensile testing?
A Universal Testing Machine (UTM) applies a gradual tensile force to a properly gripped and aligned specimen until failure. The machine records stress-strain data, helping industries evaluate material performance, durability, and safety compliance.
Looking for tensile testing services in India? Get accurate, NABL-certified material testing with advanced Universal Testing Machines (UTMs) today!
Registration & Certifications
Synergistically incentivize effective imperatives through fully researched intellectual capital. Appropriately fashion client-based.
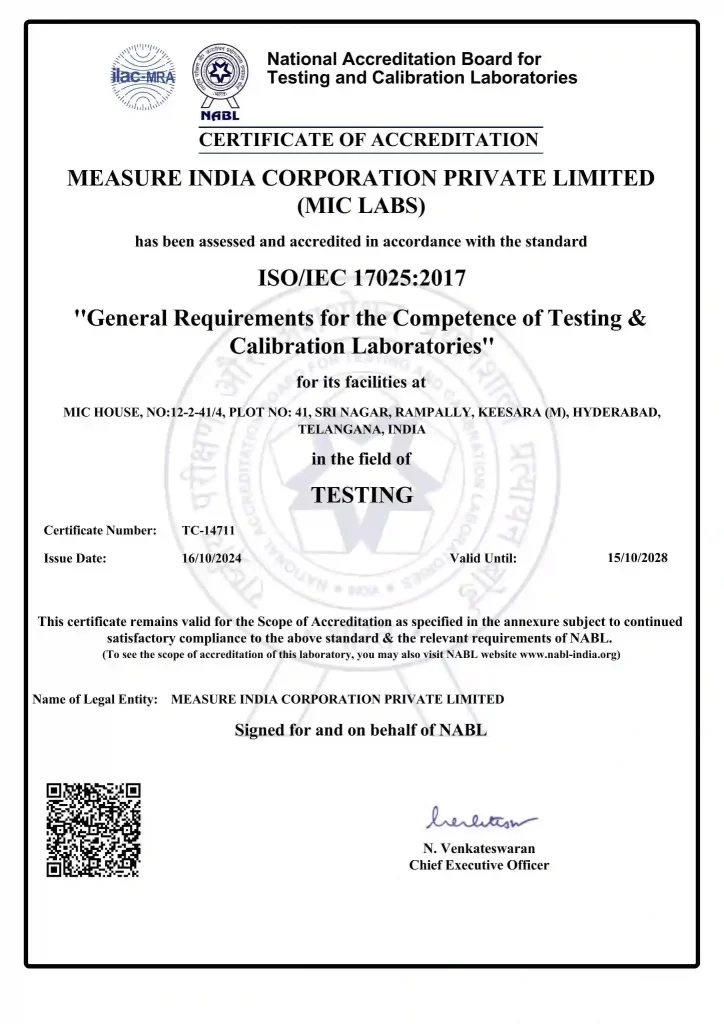
Accredited by NABL
(National Accreditation Board for Testing and Calibration Laboratories – India)
Our laboratory is accredited by NABL as it meets international standards for quality and competence. It operates in accordance with ISO/IEC 17025:2017. NABL accreditation is recognized both nationally and internationally, ensuring the laboratory’s technical competence, impartiality, and reliability.
If you are looking for NABL-accredited testing laboratories in India, our facility provides high-precision testing services in compliance with global quality standards.
Tensile Testing (Standards: ASTM E8M, ASTM E21, ASTM B557M, ASTM A770, ASTM D3039M, IS 1608 Part-1, IS 1608 Part-3, ISO 6892, ASTM D412, ASTM D638)
Compression Testing (Standard: ASTM D575)
Bend Testing (Standards: ASTM E290, IS 1599)
Low Cycle Fatigue Testing (Standard: ASTM E606)
High Cycle Fatigue Testing (Standard: ASTM E466)
Fatigue Crack Growth Rate Testing (Standard: ASTM E647)
Fracture Toughness Testing (K₁C) (Standard: ASTM E399)
Fracture Toughness Testing (J₁C) (Standard: ASTM E1820)
Creep & Stress Rupture Testing (Standard: ASTM E139, E292)
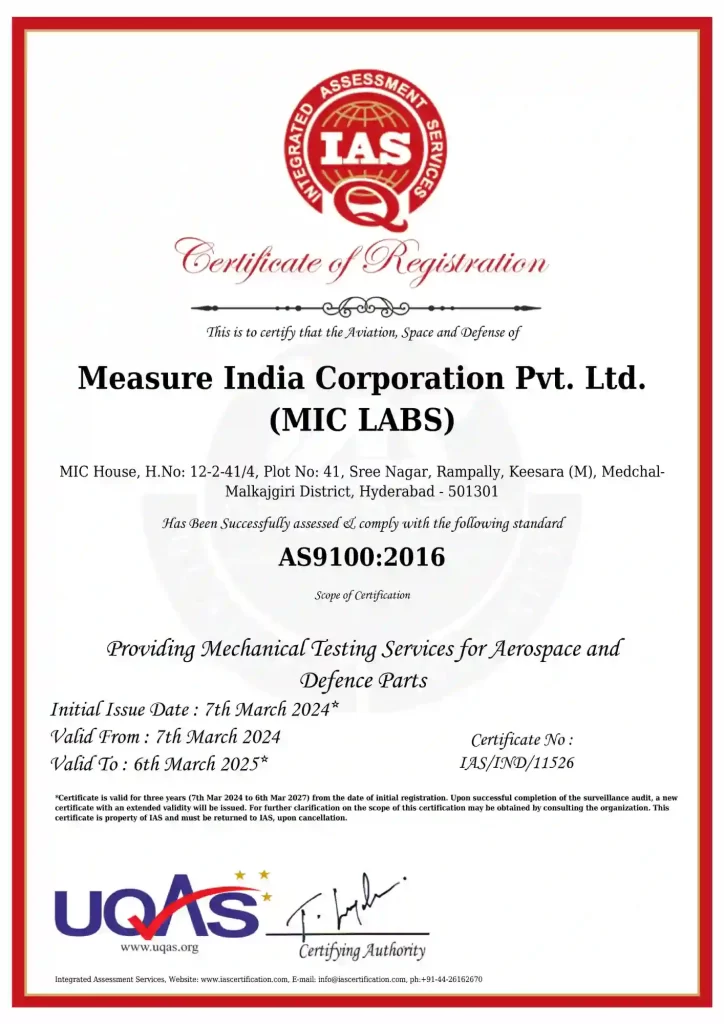
AS9100:2016 Certified
( Integrated Assessment Services )
MIC Labs is certified by IAS in accordance with AS9100:2016, meeting international standards for quality and competence. AS9100:2016 is recognized both nationally and internationally, signifying a laboratory’s technical competence, impartiality, and reliability.
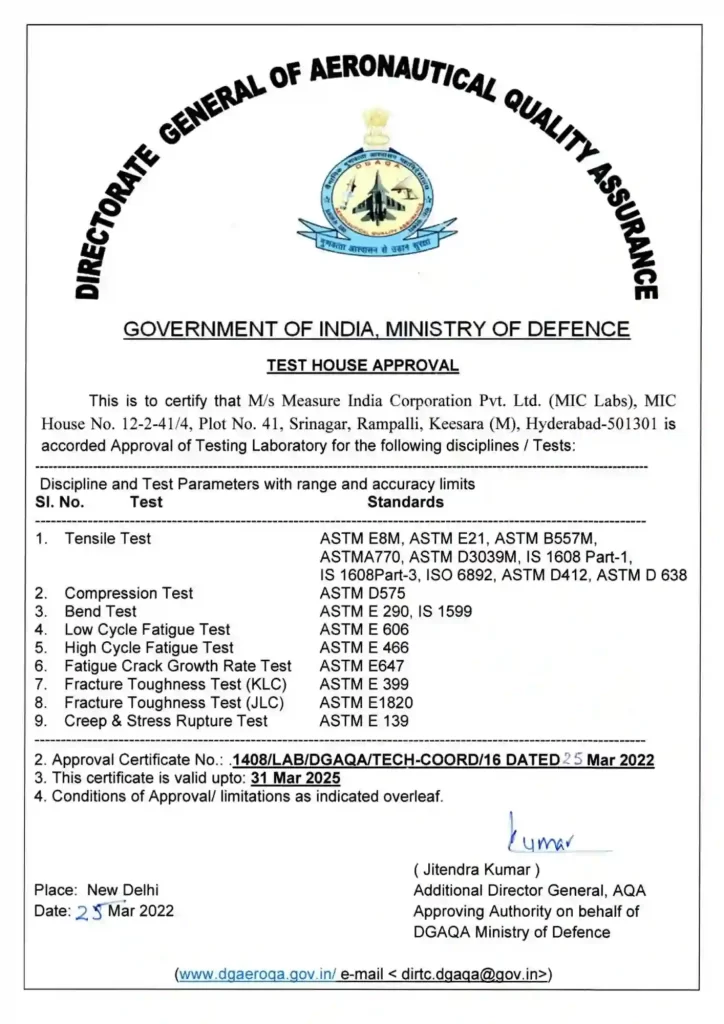
Approved by DGAQA
( Directorate General of Aeronautical Quality Assurance )
MIC Labs is approved by DGAQA ensuring that our laboratory meets the stringent standards required for testing in the aerospace and defense sectors. This approval reflects our technical competence and commitment to delivering reliable and precise results.
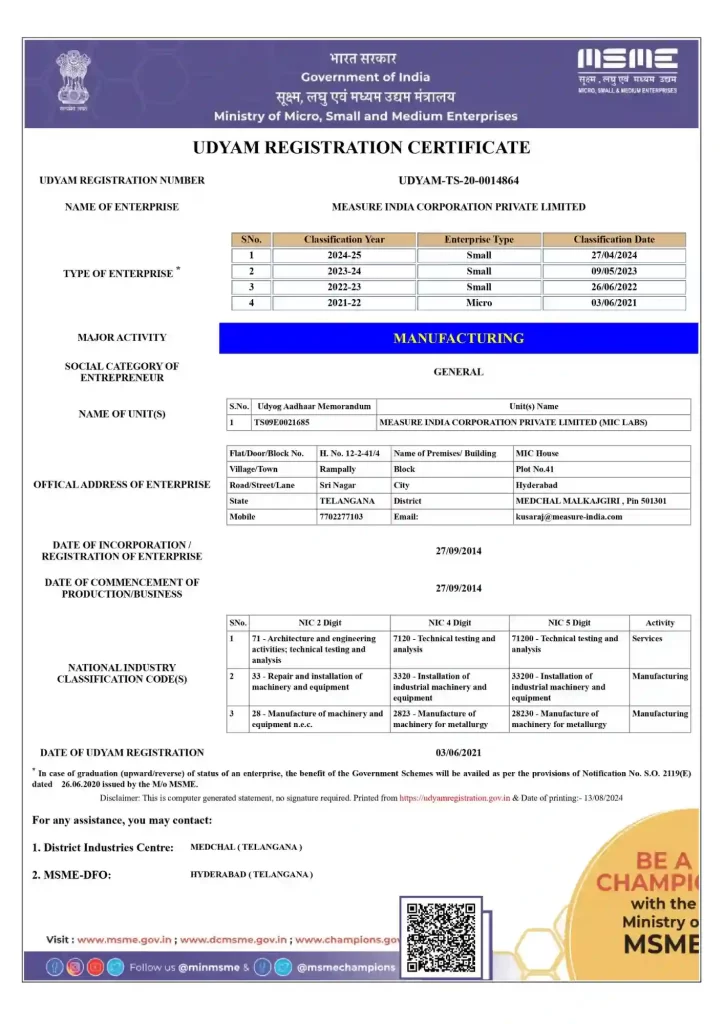
Registered by UDYAM
Measure India Corporation Pvt Ltd is UDYAM registered, recognizing us as a legitimate micro, small, or medium enterprise (MSME) in India. This registration highlights our commitment to quality and compliance with industry standards.
Why Choose Us
We have 20 years of experience in providing material testing systems and offering testing services with great confidence.
- 90+ Products
- 500+ Customers
- 35+ Team Size
- Expertise in guiding and working with top-notch researchers and engineers
- World-class mechanical testing laboratory
Mechanical Testing Lab Services & Universal Testing Machines Suppliers in India
“With over 20 years of experience, Measure India Corporation Pvt Ltd supplies Universal Testing Machines & mechanical testing services, ensuring precision, reliability, and compliance with ASTM, ISO, and global standards across various industries.”
Customer Satisfaction
Business Growth Every Year
500+
Active Clinets
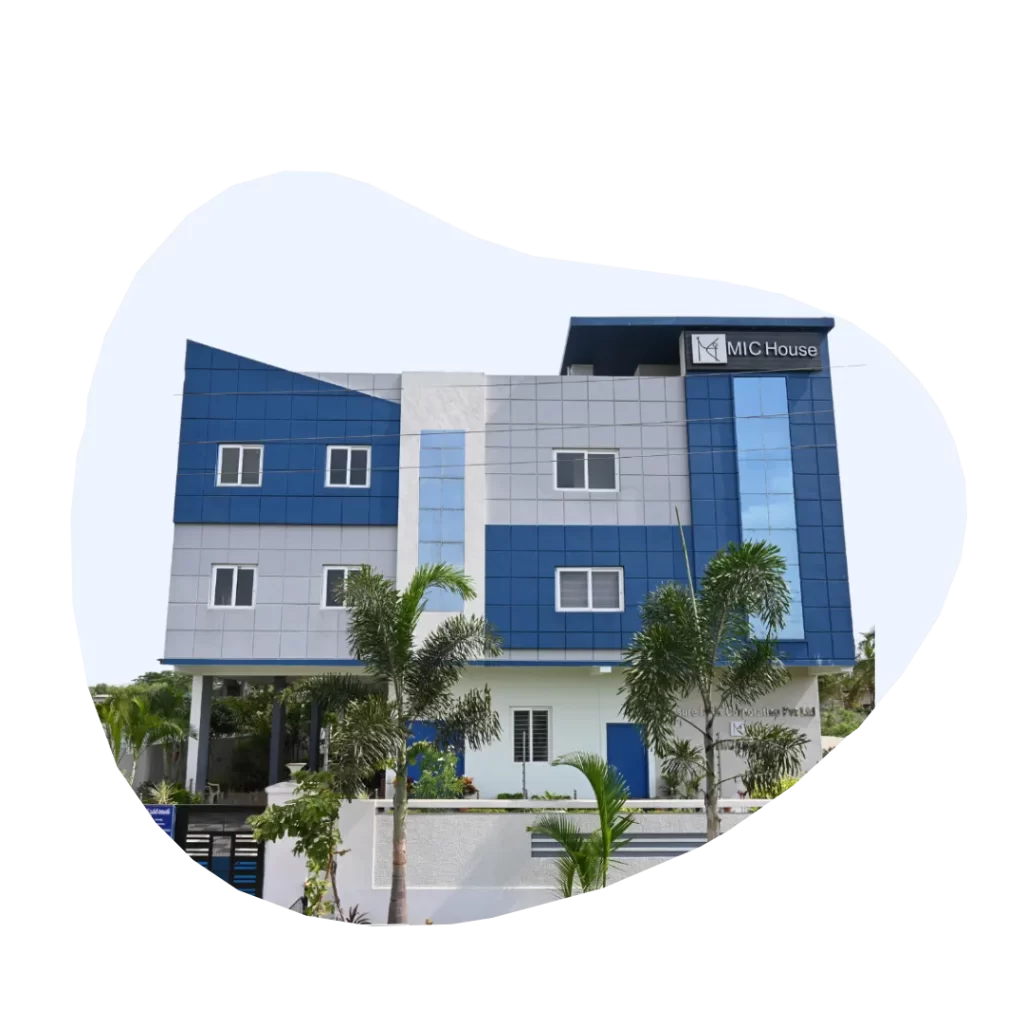
Trusted Clients
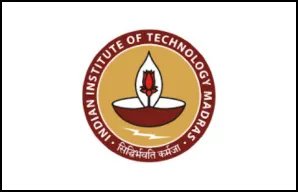
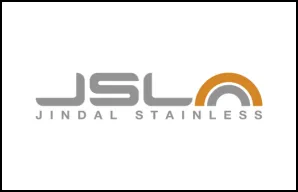
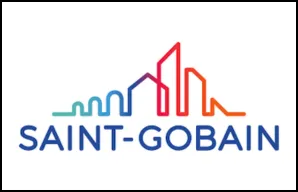
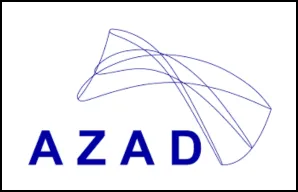
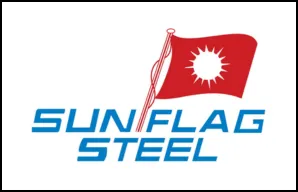
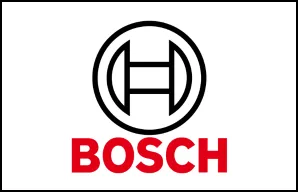
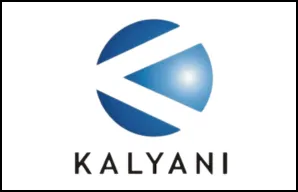
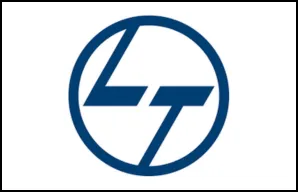
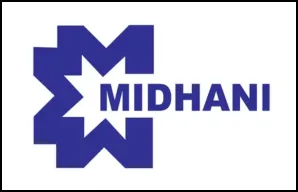
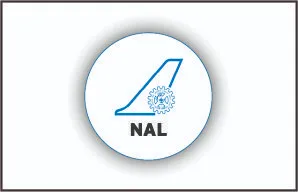
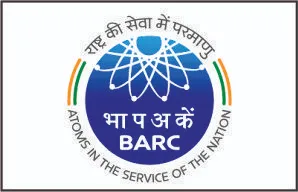
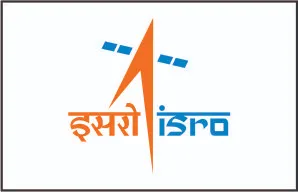
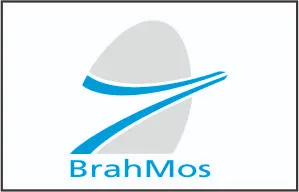
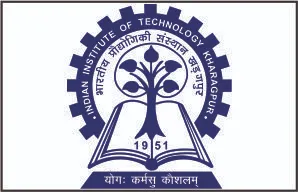
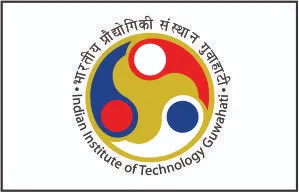
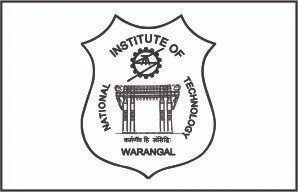
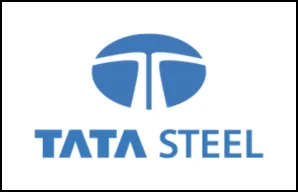
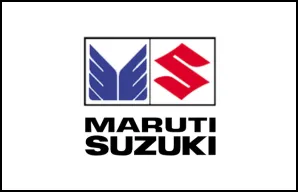
Brands We Deal
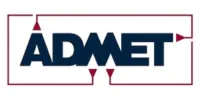
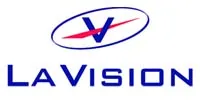
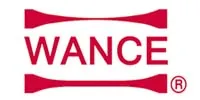
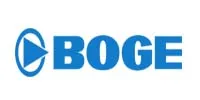
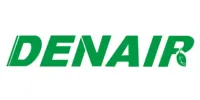
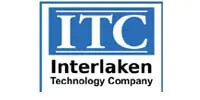
Call us Now
For Universal Testing Machine: +91 99899 21114
Air Compressors: 96767 43939
Material Testing Laboratory : +91 91000 44532
Email Us
Email: info@measure-india.com
Opening Hours
From Monday – Saturday
9:00 am to 5:30 pm
Our Location
MIC House, Plot No 41, Srinagar, Rampally,
Hyderabad, Secunderabad, Telangana 501301
Get In Touch With us
We value your inquiries and feedback! Please fill out the form below, and a member of our team will respond to you promptly.